

UNIVERSIDAD FERMÍN
TORO
FACULTAD ECONÓMICA DE CIENCIAS Y SOCIALES
ESCUELA DE
ADMINISTRACIÓN
DIRECCIÓN SAIA
DIRECCIÓN SAIA
INTEGRANTES: ROSANGELA TORRES
ASTRID ALBARRAN
ABEL FERREIRA
LUISANA SILVA
MATERIA: GERENCIA INDUSTRIAL
FEBRERO 2015
UNIDAD I
GERENCIA INDUSTRIAL
Gerencia
industrial:
El objetivo de esta materia es interpretar las teorías y enfoques
gerenciales para la optimización de los sistemas productivos en las empresas,
considerando a los individuos, la estructura organizacional, sus procesos y el
ambiente donde se desarrollada la actividad industrial, a través de la
utilización de herramientas y las distintas perspectivas de los participantes
dentro del contexto socio-económico regional y nacional.
Importancia:
· Comprende los logros u
objetivos de los individuos.
· Imparte
efectividad en los esfuerzos humanos.
· Optimiza
el insumo.
Teoría administrativa:
Teoría gerencial:

• El trabajo debe ser visto
como algo divertido, es decir que sea como un juego y este pueda ser
disfrutado.
• El trabajo es
importante, no lo eche a perder con demasiada seriedad.
• Las personas
son importantes, cada una de ellas constituye una diferencia.
Teoría del comportamiento:
Orígenes de la
Teoría del Comportamiento.
Los
orígenes de la teoría del comportamiento son los siguientes:
1.
Oposición fuerte y definitiva de las teorías anteriores.
2.
Critica severa a la teoría de las relaciones humanas y a la clásica.
3. La
incorporación de la sociología al campo de la teoría administrativa
(influenciada por la teoría del comportamiento).
(influenciada por la teoría del comportamiento).
4. En
contraposición con la teoría de la burocracia, con respecto al “modelo
maquina”.
La gerencia y administración en el siglo XXI
La historia ha demostrado que por miles de años la economía ha sido agraria. Desde el inicio de la humanidad tuvieron que trabajar en el campo para poder vivir y alimentar a sus familias. Los primeros seres humanos domesticaron la vegetación y las consecuencias de este descubrimiento fueron estremecedoras: aparecieron las primeras aldeas, los recolectores nómadas se transformaron en campesinos sedentarios, cabe destacar que es mas difícil de recuperarse de situaciones caóticas, lo que quiere decir que la decadencia equivale, cada vez más, a la muerte de las organizaciones.
Los desafíos que enfrentan la adminitación del siglo actual
es decir siglo XXI son: Competitividad global, demanda de la calidad,
lucratividad, responsabilidad social entre otros; para poder vencer estos
desafíos los administradores tienen que ser flexibles, pro-activos y concentrase
en la calidad de lo que hacen.
ASTRID ALBARRAN
UNIDAD II
Sistema de Producción

Es un conjunto de actividades dentro del
cual la creación del valor puede ocurrir. También podemos
decir que es la manera por la cual la empresa ordena sus organismos y realiza
sus operaciones de producción para lograr una interdependencia lógica entre
todas las etapas del proceso productivo.
Principales Componentes del Sistema de Producción
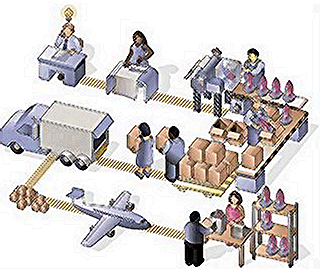
Entradas (Inputs) o insumos: Constituyen todo lo que ingresa en un
sistema para permitir que funcione. Pueden ser energía, información, materias
primas, o sea, todo y cualquier recurso que alimente el sistema. Las entradas
provienen del ambiente externo.
Salidas (outputs) o resultados: Es aquello que el sistema produce y
devuelve al ambiente externo.
Transformación: Es lo que el sistema (o sus subsistemas) realiza con las
entradas para proporcionar las salidas. Es el funcionamiento interno del
sistema.
Retroacción (feedback) o retroalimentación: Es la influencia que las salidas del
sistema ejercen sobre sus entradas, en el sentido de ajustarlas o regularlas de
acuerdo con el funcionamiento del sistema. Existen dos tipos de retroacción: la
positiva (que acelera o aumenta las entradas para ajustarlas a las salidas,
cuando éstas son mayores) y la negativa (que retarda o disminuye las entradas
para ajustarlas a las salidas, cuando éstas son menores).
Tipos de Sistema de Producción
1. PRODUCCIÓN POR TRABAJOS O BAJO PEDIDO: Es el utilizado por la empresa que
produce solamente después de haber recibido un encargo o pedido de sus
productos.
2. PRODUCCIÓN POR LOTES: Es el sistema de producción que usan las empresas que producen
una cantidad limitada de un producto cada vez, al aumentar las cantidades más
allá de las pocas que se fabrican al iniciar la compañía, el trabajo puede
realizarse de esta manera. Esa cantidad limitada se denomina lote de
producción. Es en la producción por
lotes donde el departamento de control de producción puede producir los mayores
beneficios, pero es también en este tipo de producción donde se encuentran las
mayores dificultades para organizar el funcionamiento efectivo del departamento
de control de producción.
3. PRODUCCIÓN CONTINUA: Este sistema es el empleado por las empresas que producen un
determinado producto, sin cambios, por un largo período. El ritmo de producción
es acelerado y las operaciones se ejecutan sin interrupción. Como el producto
es el mismo, el proceso de producción no sufre cambios seguidos y puede ser
perfeccionado continuamente.
C.I.16.322.828
UNIDAD III
GESTIÓN DE ALMACÉN
La gestión de almacén
La gestión de almacenes se define como el proceso de
la función logística que
trata la recepción, almacenamiento y movimiento dentro de un mismo almacén
hasta el punto de consumo de cualquier material – materias primas,
semielaborados, terminados, así como el tratamiento e información de los datos
generados.
La gestión de almacenes tiene como objetivo
optimizar un área logística funcional que actúa en dos etapas de flujo como lo
son el abastecimiento y la distribución física, constituyendo por ende la
gestión de una de las actividades más importantes para el funcionamiento de una
organización.
La gestión de almacenes es un concepto ligado a la gestión de stocks, se
trata de la gestión física de los productos almacenados. La gestión de
almacenes comprende, por tanto:
·
La ubicación de los productos en
un almacén
·
Los flujos de materiales dentro
del almacén y los métodos para el movimiento de productos
·
La trazabilidad de los productos
almacenados
·
La preparación de pedidos
(Picking)
El método estandarizado más conocido de gestión de almacenes es el
método ABC que consiste en líneas generales en clasificar en tres tipos (A, B,
C) los productos en función del nivel de rotación del producto y el nivel de
stock que se establece como consecuencia.
Importancia
y Objetivos
La gestión de almacenes consiste en garantizar el suministro continuo y oportuno
de los materiales y medios de producción requeridos para asegurar los servicios
de forma ininterrumpida y rítmica. Se sitúa en el Mapa de Procesos
Logísticos entre la Gestión de Existencias y el Proceso de Gestión de Pedidos y
Distribución. De esta manera el ámbito de responsabilidad (en cuya ampliación
recae la evolución conceptual del almacenamiento) del área de almacenes nace en
la recepción de la unidad física en las propias instalaciones y se extiende
hasta el mantenimiento del mismo en las mejores condiciones para su posterior
tratamiento.
Describir la importancia y los objetivos de una
gestión dependen directamente de los fundamentos y principios que enmarcan la
razón de ser de la misma, sin embargo tal como lo observamos en la gráfica
anterior sobre el "debe ser almacenado" quien formula las cuestiones
de fundamento y principio es la gestión de inventario o existencia, y en estas se basa la gestión de almacenes
para tener una gran importancia y unos claros objetivos.
Los objetivos que debe plantearse una gestión de
almacenes son:
OBJETIVOS
|
Rapidez
de entregas
|
Fiabilidad
|
Reducción
de costes
|
Maximización
del volumen disponible
|
Minimización
de las operaciones de manipulación y transporte
|
Los
beneficios (que justifican su importancia) son:
BENEFICIOS
|
Reducción
de tareas administrativas
|
Agilidad
del desarrollo del resto de procesos logísticos
|
Optimización
de la gestión del nivel de inversión del circulante
|
Mejora
de la calidad del producto
|
Optimización
de costes
|
Reducción
de tiempos de proceso
|
Nivel
de satisfacción del cliente
|
Funciones
de un almacén
Aunque el derrotero de funciones de un almacén
depende de la incidencia de múltiples factores tanto físicos como
organizacionales, algunas funciones resultan comunes en cualquier entorno,
dichas funciones comunes son:
- Recepción de Materiales.
- Registro de entradas y salidas del Almacén.
- Almacenamiento de materiales.
- Mantenimiento de materiales y de almacén.
- Despacho de materiales.
- Coordinación del almacén con los departamentos de control de
inventarios y contabilidad.
Principios
de la Gestión de Almacén
Como ya ha sido tratado en el módulo de administración de inventarios, todo manejo y almacenamiento de materiales y productos
es algo que eleva el costo del producto final sin agregarle valor, en teoría es
un mal necesario, razón por la cual se debe conservar el mínimo de existencias
con el mínimo de riesgo de faltantes y al menor costo posible de operación.
Para llevar a cabo tal empresa, la gestión de
almacenes debe establecer y regirse por unos principios comunes fundamentales,
conocidos como principios del almacén (aplicables
a cualquier entorno):
- La custodia fiel y eficiente de los materiales o productos debe
encontrarse siempre bajo la responsabilidad de una solo persona en cada
almacén.
- El personal de cada almacén debe ser asignado a funciones
especializadas de recepción, almacenamiento, registro, revisión, despacho
y ayuda en el control de inventarios.
- Debe existir un sola puerta, o en todo caso una de entrada y otra
de salida (ambas con su debido control).
- Hay que llevar un registro al día de todas las entradas y salidas.
- Es necesario informar a control de inventarios y contabilidad todos
los
movimientos del almacén (entradas y salidas), la programación y control de producción sobre las existencias. - Se debe asignar una identificación a cada producto y unificarla por
el nombre común y conocido de compras, control de inventario y producción.
- La identificación debe estar codificada.
- Cada material o producto se tiene que ubicar según su clasificación
e identificación en pasillos, estantes, espacios marcados para facilitar
su ubicación. Esta misma localización debe marcarse en las tarjetas
correspondientes de registro y control.
- Los inventarios físicos deben hacerse únicamente por un personal
ajeno al almacén.
- Toda operación de entrada o salida del almacén requiriere
documentación autorizada según sistemas existentes.
- La entrada al almacén debe estar prohibida a toda persona que no
esté asignada a él, y estará restringida al personal autorizado por la
gerencia o departamento de control de inventarios.
- La disposición del almacén deberá ser lo más flexible posible para
poder realizar modificaciones pertinentes con mínima inversión.
- Los materiales almacenados deberá ser fáciles de ubicar.
- La disposición del almacén deberá facilitar el control de los
materiales.
- El área ocupada por los pasillos respecto de la del total del
almacenamiento propiamente dicho, debe ser tan pequeña como lo permitan
las condiciones de operación.
Proceso de
gestión de almacenes
El mapa de proceso de
la gestión de almacenes se compone de dos ejes transversales que representan
los procesos principales
- Planificación y Organización y Manejo de la
información y tres subprocesos que componen la gestión de
actividades y que abarca: La recepción, el almacén y el movimiento.
Planificación y organización
El proceso de
planificación y organización es de carácter estratégico y táctico, dado que
tiene que brindar soluciones de recursos en comunión con las políticas y
objetivos generales que contempla la estrategia de la compañía, en aras de
potenciar las ventajas competitivas por las que apuesta la misma.
Recepción
El flujo
rápido del material que entra, para que esté libre de toda congestión o demora,
requiere de la correcta planeación del área de recepción y de su óptima
utilización. La recepción es el proceso de planificación de las entradas de
unidades, descarga y verificación tal y como se solicitaron mediante la
actualización de los registros de inventario.
El objetivo al que
debe tender una empresa en su proceso de recepción de mercancías es la
automatización tanto como sea posible para eliminar o minimizar burocracia e
intervenciones humanas que no añaden valor al producto. Otra tendencia
considerada como buena práctica logística es la implementación de programas de entregas certificadas que
no solo eliminan burocracia sino que reducen al mínimo las inspecciones que se
consideran imprescindibles pero que no añaden valor.
En primer lugar, el
proceso de recepción de mercancías debe cimentarse en una previsión de entradas
que informe de las recepciones a realizar en tiempo dado y que contenga,
al menos, el horario, artículos, y procedencia de cada recepción, este proceso
se conoce como cita previa ya que para procesos como entregas paletizadas se
debe contar con recursos muy específicos como montacargas, plataformas móviles,
rampas, entre otros.
Tras la descarga e
identificación, las cuales deben realizarse de manera inmediata y en zona
específica habilitada a tal efecto, las mercancías deben pasar a
almacenamiento, bien sea temporal a la espera de su ubicación definitiva, bien
sea fijo en su ubicación definitiva.
Almacén
El almacenamiento o
almacén es el subproceso operativo concerniente a la guarda y conservación de
los productos con los mínimos riesgos para el producto, personas y compañía y
optimizando el espacio físico del almacén. El almacén puede dividirse en las
siguientes zonas:
ZONAS DE UN ALMACÉN |
Recepción: zona donde se realizan las actividades del proceso de recepción |
Almacenamiento, reserva o stock: zonas destino de los productos almacenados. De adaptación absoluta a las mercancías albergadas, incluye zonas específicas de stock para mercancías especiales, devoluciones, etc |
Preparación de pedidos o picking: zona donde son ubicados las mercancías tras pasar por la zona de almacenamiento, para ser preparadas para expedición |
Salida, verificación o consolidación: desde donde se produce la expedición y la inspección final de las mercancías |
Paso, maniobra: zonas destinadas al paso de personas y máquinas. Diseñados también para permitir la total maniobrabilidad de las máquinas. Oficinas: zona destinada a la ubicación de puestos de trabajo auxiliares a las operaciones propias de almacén |
Oficinas: zona destinada a la ubicación de puestos de trabajo auxiliares a las operaciones propias de almacén |
Movimiento
Es el
subproceso del almacén de carácter operativo relativo al traslado de los
materiales/productos de una zona a otra de un mismo almacén o desde la zona de
recepción a la ubicación de almacenamiento. La actividad de mover físicamente
mercancías se puede lograr por diferentes medios, utilizando una gran variedad
de equipos de manipulación de materiales. El tipo de herramientas utilizado
depende de una serie de factores como son:
- Volumen del almacén
- Volumen de las mercancías
- Vida de las mercancías
- Coste del equipo frente a la finalidad
- Cantidad de manipulaciones especiales y expediciones
requeridas
- Distancia de los movimientos
Información
Si bien la función principal de la Gestión de Almacenes es la eficiencia y efectividad en el flujo físico, su consecución está a expensas del flujo de información, este es un eje transversal de los procesos de gestión logística, y la gestión de almacenes no son la excepción. Debe ser su optimización, por tanto, objetivo de primer orden en la Gestión de Almacenes. Su ámbito se extiende a todos los procesos anteriormente descritos – Planificación y organización, recepción, almacén y movimiento – y se desarrolla de manera paralela a ellos por tres vías:
- Información para gestión.
- Identificación de ubicaciones.
- Identificación y trazabilidad de mercancías
LUISANA SILVA
CAPACIDAD Y LOCALIZACIÓN DE LA PLANTA
Capacidad
La capacidad de la empresa se define,
entonces, como el output por periodo que puede obtenerse con los recursos
actuales en condiciones de operaciones normales. Este concepto no debe
confundirse con la capacidad pico y con el volumen. El volumen es la cantidad
real de producción durante cierto periodo.
La capacidad pico representa la
cantidad eventual máxima de la operación que puede conseguirse sólo durante un
periodo de tiempo muy corto, considerando la inclusión de tiempo extra,
trabajadores adicionales y políticas especiales para un mayor volumen.
La primera decisión importante que
debe tomar la empresa cuando decide fabricar un nuevo producto o atender un
mayor número de clientes con los productos existentes es aumentar la capacidad.
Por el contrario cuando la demanda de los productos disminuye, es posible que
tenga que disminuir la capacidad. En este sentido, el objetivo de la capacidad
de una fábrica es satisfacer de la forma más eficiente y en el momento oportuno
la cantidad de producto requerido por el mercado.
La planificación de la
capacidad
La decisión de incrementar la
capacidad comprende fuertes inversiones de capital y tiene consecuencias
irreversibles a largo plazo. Consta de las siguientes etapas:
A) Previsión de la demanda:
Esta se caracteriza por:
- Tener por lo menos 5 años de
duración.
- Incluir los posibles productos
nuevos que incorporará la empresa, así como aquellos que serán abandonados.
- Reflejar el cambio en la estrategia
competitiva de la empresa.
- Recoger los cambios tanto
demográficos como tecnológicos.
B) Análisis del sector:
Un sector industrial evoluciona de
acuerdo con una curva de coste unitario en forma de U, la empresa debe tener en
cuenta en que parte de la curva se encuentra la capacidad del sector, es decir,
en la parte de costes decrecientes o en la parte de costes crecientes.
1. En situación de costes
decrecientes, las empresas tienden a incrementar la capacidad, llevando a cabo
alguna de las siguientes actuaciones:
- Construir a gran escala.
- Explotar ventajas de economías de
escala.
- Construir nuevas plantas y que estas
sean de gran tamaño.
2. En situación de costes crecientes,
las empresas suelen tomar las siguientes decisiones:
- Construir fábricas de pequeña
escala.
- Endeudarse para explotar
instalaciones existentes.
En el caso de que la empresa se
encuentre en una situación de costes decrecientes competirá vía coste, mientras
que en situaciones de costes crecientes predominará la estrategia de
diferenciación.
C) Análisis interno de la empresa:
La dirección deberá establecer un plan
de actuación que entre otros deberá tener en cuenta lo siguiente:
- Número de trabajadores en la
fábrica.
- Turnos de fabricación.
- Preferencias de localización.
- Los condicionantes económicos
estratégicos.
Factores que determinan la
capacidad
Los principales factores que
determinan la capacidad en la empresa son:
1.- Instalaciones: la estructura del local, las
condiciones de salubridad, los costes de transporte y la dimensión, entre
otros, afectan directamente a la capacidad presente y futura de la planta.
2.- Trabajadores: la cualificación de los trabajadores,
la rotación de los puestos, la motivación, así como cualquier política de
gestión de personal que incida sobre la productividad de los mismos o que
suponga una mejora en la realización del trabajo son también factores
relevantes en la determinación de la capacidad de la empresa.
3.- Productos: la estandarización de los componentes
y la producción a gran escala facilita que las plantas tengan una gran
capacidad productiva, sin embargo una producción muy diversificada condiciona
el crecimiento de las instalaciones en el mismo lugar físico.
4.- Procesos: los procesos rígidos permiten un
mayor volumen de producción generalmente que los procesos flexibles.
5.- Factores de producción: no es lo mismo fabricar productos con
una elevada calidad dirigidos a segmentos con elevado poder adquisitivo que
fabricar productos con un diseño estándar dirigidos a un mercado de masas.
6.- Factores externos: las políticas gubernamentales, así
como el cambio en las necesidades del mercado condicionan la capacidad.
Pasos
para decidir sobre la Capacidad
1. Establecer una medida
adecuada sobre la capacidad
2. Prever la demanda
3. Determinar la capacidad
de producción necesaria
4. Establecer un conjunto de
alternativas
5. Evaluar las alternativas
y decidir Planificación y cálculo de la capacidad
Localización
Es
el lugar donde se realiza la actividad productiva; esto es el emplazamiento
donde deben desplazarse los factores productivos y donde se obtienen los
productos, que a su vez son transportados hasta el mercado.
La
localización correcta de una planta es tan importante para su buen éxito como
la selección de un buen proceso. Debe estudiarse cuidadosamente no sólo la
mayoría de los factores tangibles como las disponibilidades de mano de obra y
las fuentes de materia prima, sino también, un gran número de factores intangibles
que son más difíciles de evaluar. La selección de una planta debe basarse en un
estudio muy detallado en el que deben tomarse en cuenta todos los factores
tanto como sea posible. A menudo un estudio así, es costoso, pero las falsas
economías en este concepto pueden conducir a grandes pérdidas en el futuro.
En el estudio de localización se involucran dos aspectos diferentes:
- Macrolocalización: Es decir, la selección de
la región o zona más adecuada, evaluando las regiones que preliminarmente
presenten ciertos atractivos para la industria que se trate.
- Micro localización: Es decir, la selección específica del sitio o terreno que se encuentra en la región que ha sido evaluada como la más conveniente.
Factores que
afectan a la localización de Planta
Una buena
localización de una instalación requiere de un estudio detallado de los
factores que pueden afectar desde el punto de vista mundial, nacional, o
departamental; debido a que la misma obedece al grado de desarrollo de las
organizaciones, ya que mientras más grandes sean, más cuidadosos serán los
estudios que se deben tomar en cuenta a la hora de ampliar sus operaciones.
Partiendo de este criterio, los factores que intervienen en el estudio de
ubicación de una instalación son las siguientes:
· Las fuentes de
abastecimiento de materias primas: Ciertas
empresas se localizan próximas a los lugares en los que se obtienen sus
materias primas o sus proveedores; considerándose, para ellos, los siguientes
aspectos: la disponibilidad y seguridad de suministro actual y futuro, el usos
de posibles sustitutos, y la calidad y costos de los suministros.
· Los mercados: La localización de los clientes es un factor
importante debido a que permite obtener una estrecha relación con los clientes.
La localización de la competencia también forma parte de las consideraciones
estratégicas que contemplan los servicios y sus competidores.
· Transporte: El lugar de la instalación, dependerá de los
costos relativos de transporte de materias primas y productos terminados, desde
y hasta los centros de distribución. En general, el costo de transporte es
directamente proporcional a la distancia y al volumen de carga transportada, y
en todo caso se debe tratar de que este costo sea el más bajo posible.
· La mano de obra: Aunque este perdiendo peso en entornos
productivos tecnológicamente desarrollados, suele seguir siendo uno de los
factores importante en las decisiones de localización, sobre todo para empresas
de trabajo intensivo.
· Los suministros
básicos: Cualquier
instalación necesita de suministros básicos como el agua y la energía, por ello
es especialmente critico en las plantas de fabricación.
· La calidad de
vida: Es un
factor apreciado y considerado por las empresas en la localización de
instalaciones, pues influye en la capacidad de atraer y retener el personal,
resultando mas critico en empresas de alta tecnología o en las dedicadas a la
investigación.
· Las condiciones
climatológicas de la zona: El proceso
productivo puede verse afectado por la temperatura, el grado de humedad, entre
otros. Se incrementa costos por implementar calefacción y/o por retrasar la
producción.
· El marco
jurídico: Las normas
comunitarias, nacionales, regionales y locales inciden sobre las empresas,
pudiendo variar con la localización. Un marco jurídico favorable puede ser una
buena ayuda para las operaciones, mientras que uno desfavorable puede entorpecer
y dificultar las mismas.
Las alternativas de
localización pueden ser de tres tipos, las cuales deberán ser evaluadas
por la empresa antes de tomar una
decisión definitiva:
1. Expandir una instalación existente: Esta opción sólo será posible si existe suficiente espacio para
ello. Puede ser una alternativa atractiva cuando la localización en la que se
encuentra tiene características muy adecuadas o deseables para la empresa.
Generalmente origina menores costes que otras opciones, especialmente si la
expansión fue prevista cuando se estableció inicialmente la instalación.
2. Añadir nuevas instalaciones en nuevos lugares: A veces ésta puede resultar una opción más ventajosa que la
anterior (por ejemplo si la expansión provoca problemas de sobre
dimensionamiento o de pérdida de enfoque sobre los objetivos de las operaciones). Otras veces es simplemente la única opción
posible. En todo caso, será necesario considerar el impacto que tendrá sobre
el sistema total de instalaciones de la empresa.
Decisión de localización.
Podemos distinguir cinco tipos de
estrategias:
1) Estrategia de fábrica de producto cada
planta de la empresa se dedica a la fabricación de un único producto (o de una
línea de productos) y sirve a la totalidad del mercado de la empresa. Como
ejemplo, si una empresa fabrica 3 productos puede destinar una planta para cada
uno de ellos y cada planta va a atender a todo el mercado.
Esta estrategia es la más apropiada
para conseguir economías de escala.
2) Estrategia de fábrica de mercado cada
planta de la empresa fabrica toda la gama o linea de productos y sirve a un
área geográfica determinada, no a todo el mercado.
Ej: una empresa tiene tres plantas, en
cada una de las cuales se fabrican todos los productos de la empresa pero cada
planta sirve por ejemplo a una comunidad autónoma.
3) Estrategia de fábrica producto mercado
es una combinación de las dos anteriores. En este caso cada planta fabrica uno
o muy pocos productos y atiende a un área concreto.
4) Estrategia de fábrica de aplicaciones
generalizadas que consiste en tener una planta dedicada a la fabricación de
todo tipo de productos según fluctué la demanda.
5) Estrategia de fábrica de procesos en
cada planta se realiza una parte del proceso productivo, siendo cada planta
suministradora de otras plantas, siendo necesario coordinación muy detallada
para acoplar las salidas de producción de una planta con las entradas de
aquella a la que suministra.
LUISANA SILVA
UNIDAD V
CONTROL
DE CALIDAD

La calidad es el factor básico de decisión del cliente
para un número de productos y servicios que hoy crece en forma
explosiva. La calidad ha llegado a ser la fuerza más importante y
única que lleva al éxito organizacional y al crecimiento de la compañía en
mercados nacionales e internacionales. El control de calidad de los productos es el proceso por
el cual se establecen y se cumplen unas normas que aseguran el cumplimiento de
las especificaciones del producto.
El proceso de control sigue siete etapas, que son las siguientes:
· Establecer el objeto del control.
Elegir una unidad de medida.
· Establecer el valor normal o estándar
de la especificación a controlar.
· Establecer un instrumento de medida.
· Realizar la medición de la magnitud en
la unidad elegida.
· Interpretar las diferencias entre el
valor real y el valor normal o estándar.
·Actuar sobre las diferencias
encontradas.
HERRAMIENTAS
DE CONTROL DE CALIDAD

Para
que el control de calidad dentro de una determinada empresa, logre un resultado
óptimo es necesario que esta implemente un ideal de compromiso con la calidad
dentro de sí misma. Es recomendable también la disposición de un trabajador
capacitado que verifique los procesos.
Podemos utilizar diferentes herramientas para alcanzar la
calidad de nuestro producto o servicio:
- La versión más actual es la norma ISO 9001-2000 y es a la que toda empresa competitiva debiera de aspirar, para así poder obtener permanencia. Esta propone, mediante mejoras en la organización de la empresa que a todos benefician, unos sencillos, probados y geniales principios para la calidad final del producto.
Esta
ley plantea que para optimizar la producción con los materiales y los medios
existentes, es necesario mejorar la organización y los medios de producción,
considerándolos un todo. Para ello se deben seguir los siguientes principios:
- Liderazgo, participación
- Gestión
- Procesos
- Análisis de datos
- Mejora continua
- Gestión
- Procesos
- Análisis de datos
- Mejora continua
-Hoja para recolectar Datos: Se efectúa de manera cuidadosa y exacta, y
para ello lo mejor es utilizar planillas. Esto facilita el análisis de los
datos, a su vez permite llevar un control de productos defectuosos, estudiar
las causas que originan lo defectos o realizar una revisión global de un
producto.
-Histogramas:
Es una resumen gráfico de la variación de un conjunto de datos, lo cual nos
permite ver pautas que son difíciles de observar en una tabla numérica.
-Diagrama
de Pareto: Cuando existe falta de calidad en la Ley del 80-20 dice que los
factores que contribuyen a un mismo efecto es poco, un 20% es responsable de la
mayor parte de este efecto. Este es utilizado para priorizar las causas que lo
generan, mediante una representación gráfica.

-Diagrama
causa y efecto (diagrama de Ishikawa): Es una herramienta que ayuda a
identificar, clasificar posibles causas tanto de problemas como de
características de la calidad. Se elabora colocando una línea en la que se
colocara el problema y serán distribuidas las causas principales haciendo una
línea inclinada que tendrá como raíz la línea del problema, también se puede
añadir subcausas en las líneas verticales de las causas.
-Diagrama
de Dispersión: se utiliza para verificar que dos variables se encuentren
relacionadas
-Gráficos
de Control: permiten determinar si la variabilidad de un proceso es
constante o presenta fluctuaciones.
-Estratificación:
Es la separación de daros en categorías o clases. Los datos observados en un
grupo dado comparte unas características comunes que definen la categoría.
-Diagrama
de Flujo: es una representación gráfica de la secuencia de pasos a realizar
para producir un cierto resultado, que puede ser un producto material, una
información, servicio o una combinación de los tres.
-Calidad Total: Este método está basado en hacer el
procedimiento establecido sea llevado a cabo con excelencia para realizar las
actividades bien en el primer intento y de esta manera mino rizar el utilizado
tiempo y ahorrar materia prima.
Por normalización
se entiende el proceso de formulación, elaboración, la aplicación y
mejoramiento de las normas existentes que se aplican a las diversas actividades
económicas, industriales o científicas, con el objeto de ordenarlas y
mejorarlas. Los propósitos principales de la normalización son la
simplificación, la unificación y la especificación.
La ISO es un
órgano consultivo de la Organización de las Naciones Unidas (ONU), que tiene su
sede en Ginebra (Suiza), cuya función principal es la de contribuir al fomento
y desarrollo internacional de la normalización, para facilitar el intercambio
mundial de productos, bienes y servicios, mediante la colaboración científica,
tecnológica y técnica en el campo administrativo, industrial y económico,
manteniendo La ISO en contacto con las universidades, centros científicos y
tecnológicos.
Su estructura interna está compuesta por un Consejo de la Organización
encargado de la aprobación de los proyectos de normas, subordinados a éste se
han creado ciento setenta y seis (176) comités permanentes llamados Comités
Técnicos ISO (ISO/TC) cuya función es la de estudiar los principios científicos
de la normalización, a cada Comité Técnico se le adjudica un número de orden y
un nombre que refleja el perfil y la especialización a que se dedica.

NORMAS ISO:
Las Normas ISO son creadas para satisfacer necesidades en los campos
económico, financiero, industrial y técnico, administración, comercio y
servicios, siendo el resultado de un consenso internacional emanado de los
diferentes Comités Técnicos creados para tal fin. Hasta el momento se tiene un
número definido de estos, que se pueden identificar según la especialidad de su
dedicación.
FUNCIONES Y OBJETIVOS:
Las funciones y
objetivos de la ISO son las siguientes:
- La elaboración, discusión y presentación de los
proyectos de normas técnicas internacionales.
- Facilitar la utilización de las nuevas normas
para ser empleadas internacionalmente y en la esfera local de. cada
nación.
- Coordinar para los países miembros as
recomendaciones necesarias para la unificación de criterios de las .normas
ISO nacionales en cada país.
- Elaboración de las normas internacionales con
el apoyo, participación y aceptación de todos sus miembros.
- Colaborar activamente con organizaciones
internacionales dedicadas a la promulgación de la normalización.
ESTANDARIZACION:
Es un proceso dinámico por el cual se
documenta los trabajos a realizar, la secuencia, los materiales y herramientas
de seguridad a usar en los mismos, facilitando la mejora continua para lograr
niveles de competitividad mundial.

CICLO SDCA:
El ciclo de control o SDCA (Standardize-Do-Check-Act), su objetivo es mantener un proceso bajo los estándares establecidos, con lo que la
fase de estandarización se limita al establecimiento de un estándar, la de
ejecución es aplicarlo, la de verificación es la comprobación periódica de que
se respeta efectivamente y el ajuste es devolverlo al estándar en caso de que
se hubiera detectado que no estaba siendo así.
Los pasos básicos que deben seguirse para
mantener la situación de mejora alcanzada mediante la aplicación del ciclo
PDCA.
Aplicación: Las siglas SDCA corresponden a:
- S (STANDARDISE): Estandarizar
Estandarización de procesos definidos en el
proceso de mejora PDCA.
- D (DO): Realizar
Llevar a cabo los estándares establecidos en el
ciclo de mejora.
- C (CHECK): Comprobar
Comprobar la eficacia de los estándares definidos.
- A (ACT): Actuar
Actuar sobre los estándares definidos en
el caso que los resultados de la ejecución de los mismos no obtuviesen los
resultados definidos, así como en el momento de percibir posibilidades de
mejora.

CICLO PDCA:
El ciclo PDCA es la sistemática más
utilizada para implantar un sistema de mejor continua. A continuación vamos a
explicar que es lo que representa, cómo funciona y su relación con algunas
normas ISO.
El nombre del Ciclo PDCA viene de las
siglas Planificar, Hacer, Verificar y Actuar, en inglés Plan, Do, Check, Act.
También es conocido como ciclo de mejora continua o Círculo de Deming, por ser
Edwards Deming su autor. Esta metodología describe los cuatro pasos esenciales
que se deben llevar a cabo de forma sistemática para lograr la mejora continua.
Las cuatro etapas que componen el ciclo son las
siguientes:
1. Planificar (Plan): Se buscan las actividades susceptibles de
mejora y se establecen los objetivos a alcanzar. Para buscar posibles mejoras
se pueden realizar grupos de trabajo, escuchar las opiniones de los
trabajadores, buscar nuevas tecnologías mejores a las que se están usando
ahora, etc.
2. Hacer (Do): Se realizan los cambios para implantar la
mejora propuesta. Generalmente conviene hacer una prueba piloto para probar el
funcionamiento antes de realizar los cambios a gran escala.
3. Controlar o Verificar (Check): Una vez implantada la mejora, se deja un
periodo de prueba para verificar su correcto funcionamiento. Si la mejora no
cumple las expectativas iniciales habrá que modificarla para ajustarla a los
objetivos esperados.
4. Actuar (Act): Por último, una vez finalizado el periodo
de prueba se deben estudiar los resultados y compararlos con el funcionamiento
de las actividades antes de haber sido implantada la mejora. Si los resultados
son satisfactorios se implantará la mejora de forma definitiva, y si no lo son
habrá que decidir si realizar cambios para ajustar los resultados o si
desecharla.
Rosangela
Torres
C.I.16.322828
UNIDAD V
GESTIÓN DE CALIDAD
Para
comenzar, existen para la gestión de calidad, métodos mejoramiento continuo
basado en la filosofía de la calidad total, la cual se adapta a muchos
sistemas, y puede utilizar para mejorar los procesos de manufactura en búsqueda
de la gestión de calidad.
En
la actualidad se toma en cuenta al cliente y los trabajadores, en donde esta
cronología que se ha resaltado se ha visto una evolución de los procesos y los
paradigmas han cambiado para el beneficio empresarial y social en el cual todos
estamos insertos, y debemos contribuir para el mejoramientos de los procesos
gerenciales, administrativos, laborales, productivos, operativos, en cualquiera
en que estemos tenemos que contribuir.

La gestión de calidad establece los estándares y
las políticas para que todos los recursos bien sea organizacionales, físicos,
financieros, y el capital humano, sean tomados en cuenta y puedan
interrelacionarse para que la empresa pueda implementar la calidad, ya que el
fin es satisfacer las necesidades no solo de los clientes sino del capital
humano, quienes conforman a la empresa.
ABEL FERREIRA